INVESTMENT CASTING
What is Investment Casting ? Investment casting also known as lost wax casting is generally used for making complex-shaped components that require tighter tolerances, better surface finish and is much better than the other casitng processes. Investment casting can be used to manufacture products for industries like automobile, aerospace, machining tools, heavy equipements, engineering products, defence, etc.
In Godani we cast products in ferrous materials like stainless steel, mild steel, EN Series and non-ferrous materials like brass and bronze. We serve differnet industries of them are Indian Railways, Oil & Gas, Medical Implants, Indian Defence, Autombile Sector, Marine Industry, Valves, General Engineering, etc.
How it works
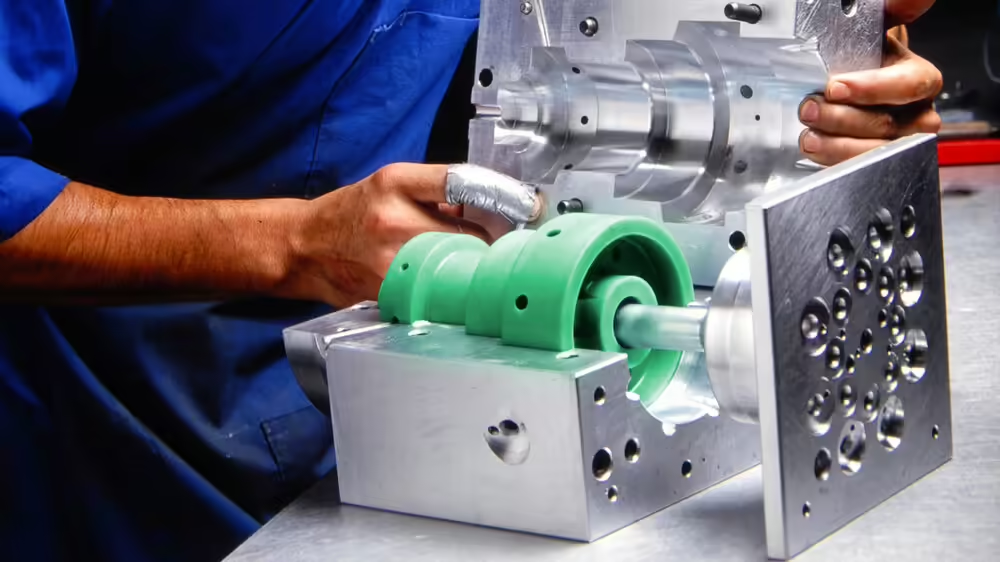
Step 1
The first step of investment casting is to create a wax pattern using an alluminium mould or die, that will look similar to the required product.
Step 2
The next step of investment casting is to attach the wax patterns to a wax riser using gate. The gate is also made up of wax. This process is known as assembly process and the assembled patterns together are called wax tree.
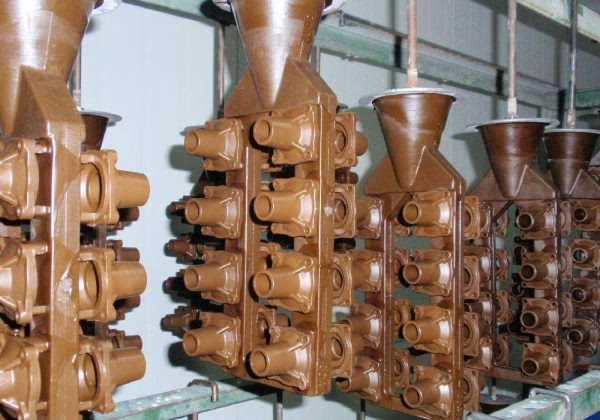
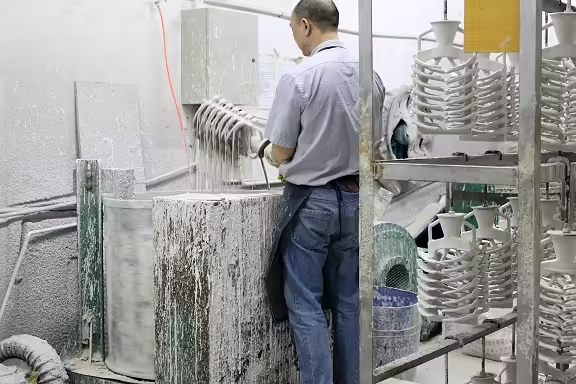
Step 3
The third step of investment casting is to dip the assembelled tree into ceramic to create a layer. And then it is left to dry. This process is repeated multiple times until it reaches the required thickness. And the final tree is called shell.
Step 4
Step four of the process is to melt the wax out of the shell using boiler machine to create cavities inside the shell.
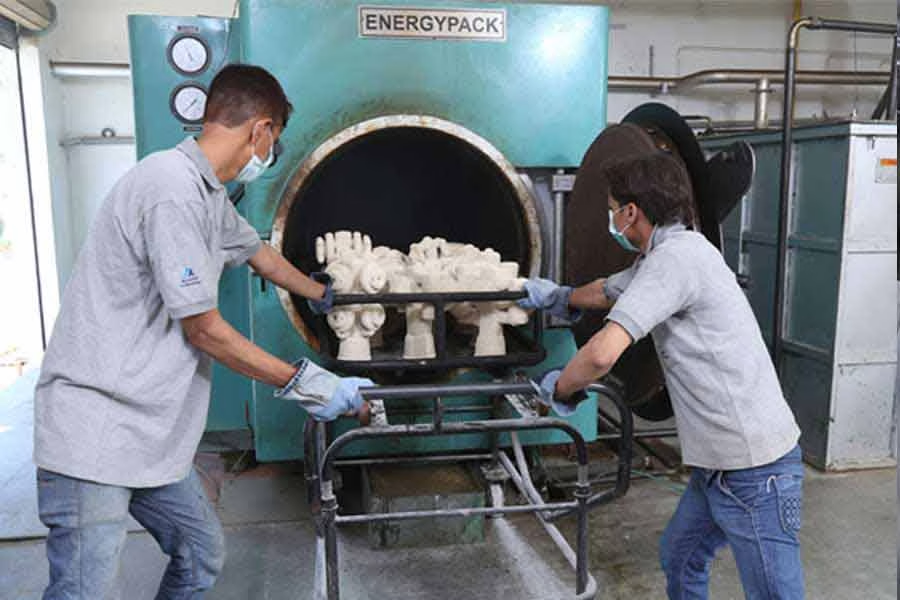
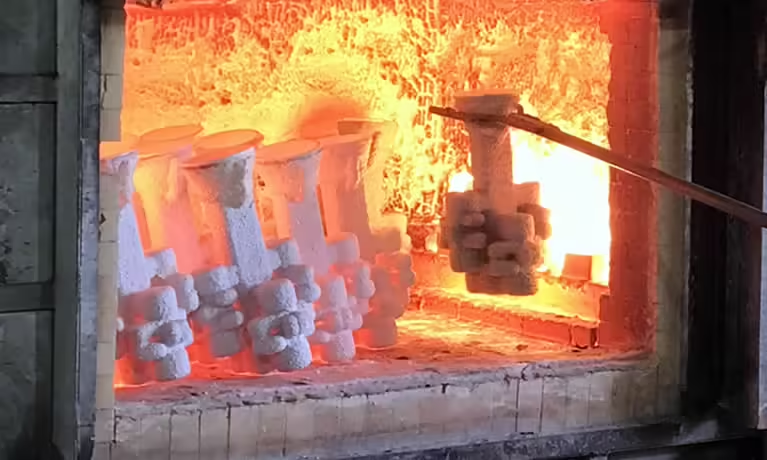
Step 5
In the next step the shells are needed to be bake to a required temperature inside an oven. The heat from the oven also metlts away the leftover wax.
Step 6
After baking the shells the molten metal is being poured into the shells manually. The shells are then given time to cool and solidification.
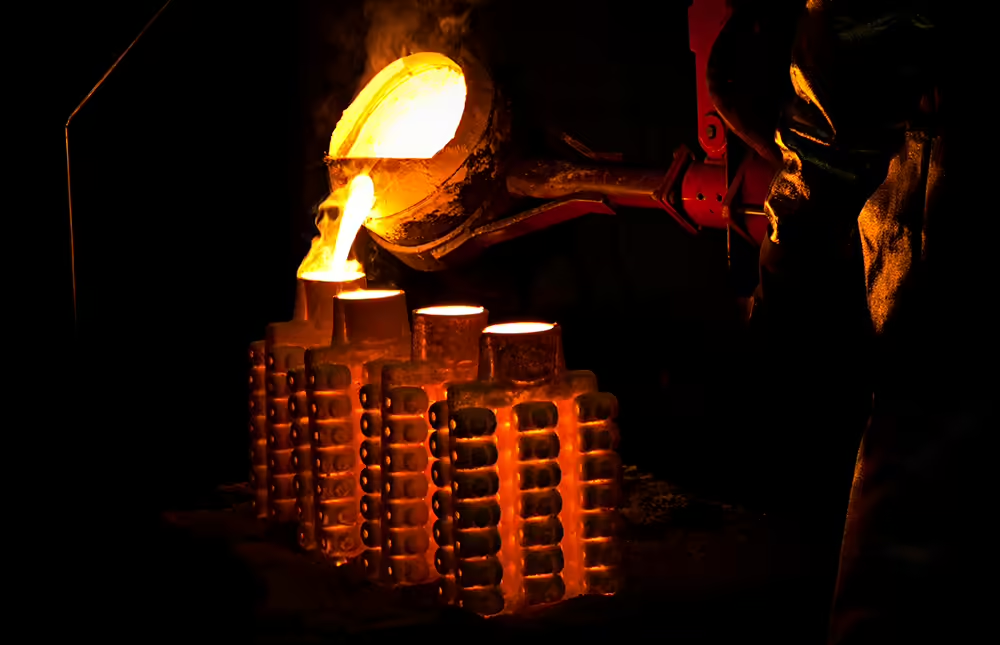
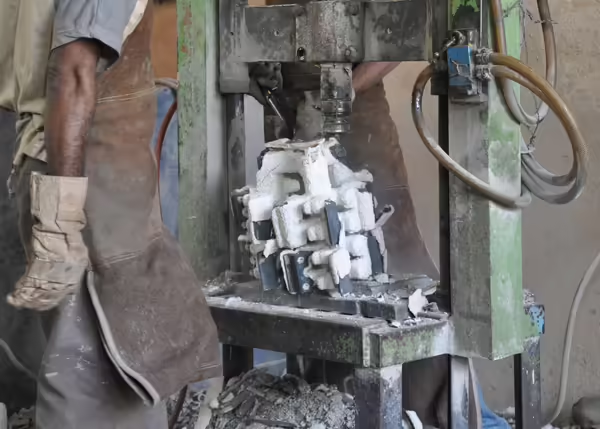
Step 7
After cooling the final process is to remove the ceramic layer from the material and finishing up the material. The ceramic layer is removed using hammer machine, which vibrates the shell strongly and then ceramic comes out. And then removes the final metal part from the riser using cutters. After that the gating part is removed using grinders.
Step 8
After final process the metal parts are sent for surface cleaning and other surface process like polishing.
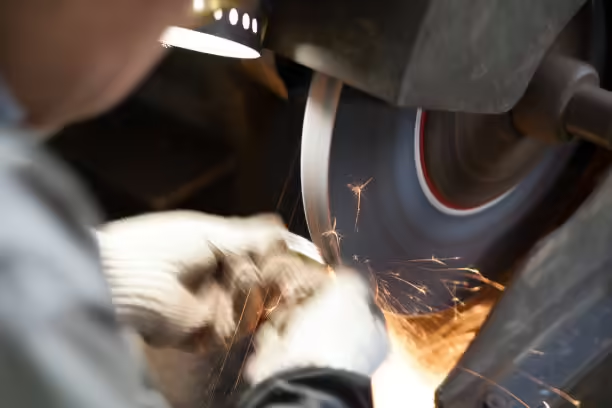